The thermal resistance, that is, the resistance encountered by heat in the heat flow path, reflects the amount of heat transfer between the medium or medium, indicating the temperature rise caused by 1 W of heat, in °C/W or K/W. An analogy can be used to explain that if the heat is equivalent to the current and the temperature difference is equivalent to the voltage, the thermal resistance is equivalent to the resistance. Generally, in the application of the LED device, the structural thermal resistance is distributed into the chip substrate, the bonding layer between the substrate and the LED holder, the LED holder, the external heat sink of the LED device, and the thermal resistance of the free space, and the thermal resistance channels are connected in series.
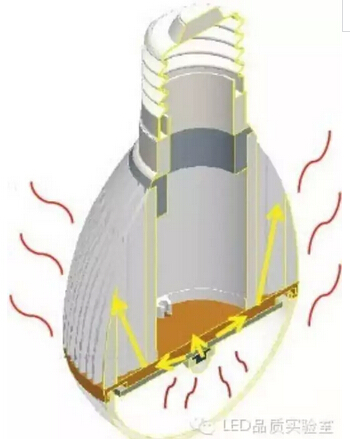
As a new energy-saving luminaire, LED luminaires only convert 30-40% of the electrical energy into light during the lighting process, and the rest become thermal energy. The existence of thermal energy urges us to pay attention to the thermal resistance of LED packaging devices. Generally, the higher the power of the LED, the more obvious the thermal effect of the LED, and the problems caused by the thermal effect are also highlighted, for example, the red shift phenomenon of the high temperature of the chip; the permanent damage of the chip due to the excessive junction temperature; the luminous efficiency of the phosphor layer is lowered. And accelerated aging; color temperature drift phenomenon; mechanical failure caused by thermal stress. These directly affect the LED's luminous efficiency, wavelength, forward voltage drop and lifetime. LED heat dissipation has become a huge bottleneck in the development of lamps.
In order to help customers understand products, overcome industry bottlenecks, and evaluate the heat dissipation level of LED package devices, Jinjian Testing LED Quality Lab has specially launched the business of “thermal resistance test and heat dissipation capability evaluation of LED package devicesâ€.
Customer service
LED packaging factory, LED lighting factory, LED chip factory, device agent
Service Content
1. Package device thermal resistance test
2. Identification of "defects" inside the packaged device
3. Structural non-destructive testing
4. Aging test characterization means
5. Contact thermal resistance test
6. Thermoelectric parameter test
Including: (1) voltage temperature change curve; (2) luminous flux temperature change curve; (3) optical power temperature change curve; (4) color coordinate temperature change curve; (5) color temperature temperature change curve; (6) efficiency temperature change curve.
Jinjian detection application example
1. Package device thermal resistance test
(1) Test method one:
In the process of testing the thermal resistance, the general heat dissipation path of the packaged product is a chip-solid layer-support or substrate-solder paste-assisted test substrate-thermal conductive connecting material.
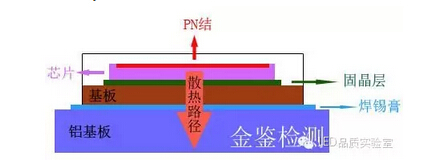
Side structure and heat dissipation path
According to the test, the thermal resistance curve can be obtained as shown below. The total thermal resistance of the test product (the entire heat dissipation path) can be read as 7.377K/W. The thermal resistance tested by this method needs to determine the thermal resistance delamination in the curve according to the structure of the test sample, and obtain the accurate thermal resistance of the packaged device. This method is more suitable for SMD package devices.
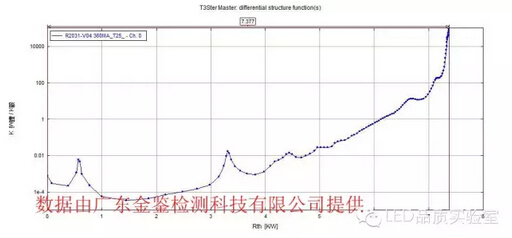
Thermal resistance curve
(2) Test Method 2:
Different from method one, the method needs to undergo two thermal resistance tests, and the obtained thermal resistance can be accurately determined to the device substrate casing without the value of the test substrate.
The difference between the two tests: the first measurement, the device directly contacts the substrate heat sink; the second measurement, the device and the substrate heat sink sandwich the thermal double-sided tape. Since the change in the two heat dissipation paths only occurs outside the device package, the boundary between the two measurements on the structure function represents the case of the device. The exact thermal resistance of the device can be derived from the curve changes shown below. This method is suitable for COB packaged devices.
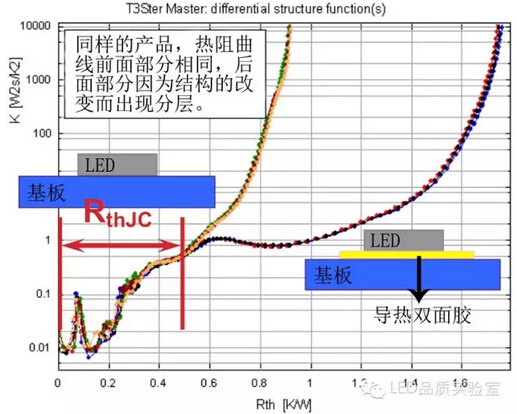
Comparison of thermal resistance curves for multiple tests
(3) Identifying the structure of the device using the structure function
Conventionally, the thermal resistance and heat capacity of the three layers of the chip, the support or the substrate, the test auxiliary substrate or the cold plate are relatively small, and the thermal resistance and heat capacity of the solid crystal layer and the thermally conductive connecting material are relatively large.
As shown in the following structure function, the closer the structure function is to the y-axis, the structure close to the active region of the chip on the actual heat flow path, and the farther away from the y-axis represents the structure farther away from the active region on the heat flow path. . The integral structure function is the heat capacity-thermal resistance function. The flat area on the curve represents the structure with large thermal resistance inside the device and small heat capacity. The steep region represents the structure with small thermal resistance inside the device and large heat capacity. In the differential structure function, the inflection point of the peak and the trough is the boundary between the two structures, which is convenient for identifying the various layers inside the device. At the end of the structure function, its value tends to a vertical asymptote, which means that the heat flow is conducted to the air layer. Because the volume of the air is infinite, the heat capacity is infinite. The x value from the origin to this asymptote is the thermal resistance of the junction to the air environment, which is the thermal resistance at steady state.
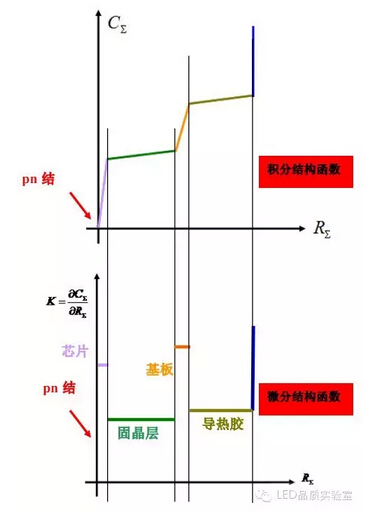
Two structural functions of the thermal resistance curve
2. Defects inside the packaged device
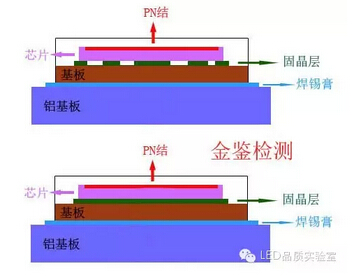
Solid crystal layer internal defect display
Comparing the cross-sectional structures of the above two devices, the solid crystal layer shows significant differences. As shown below, the left side is a normal product, and the right side is a product with a defective solid crystal layer.
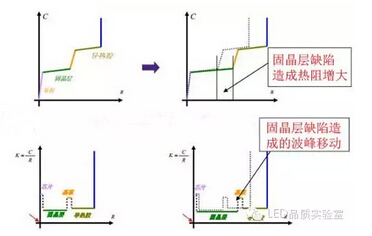
Thermal resistance caused by defects in the solid crystal layer becomes large
According to the above figure, the thermal resistance caused by the defect of the solid crystal layer increases, which affects the heat dissipation performance. The specific degree of influence is related to the size of the defect.
3. Structural non-destructive testing
For the same batch of products, take the sample test of the intact layer, edge defects and intermediate defects. The solid crystal layer of the solid crystal should be rectangular, and there are defects in the edge and the middle, then the solid crystal layer is irregular, and the pictures of the two defects are shown below.
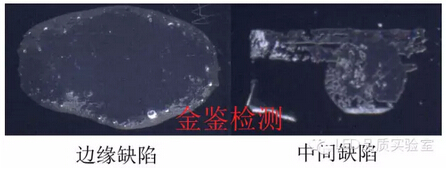
Schematic diagram of solid crystal defects
Three thermal resistance curves were tested. Since the chips tested three times are the same, the curves characterizing the chip parts in the structure function are completely coincident. As the degree of damage of the solid crystal layer increases, the thermal resistance of the structural layer gradually increases. This is caused by the cavity blocking the effective heat dissipation channel.
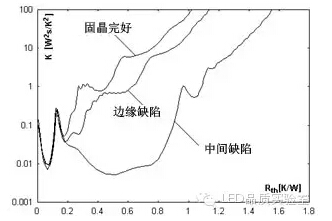
Comparison of thermal resistance of solid crystal defects
According to the test results, the gold detection can not only qualitatively find out the structure with defects, but also quantitatively determine the amount of change in thermal resistance caused by defects.
4. Aging test characterization means
The figure below shows the thermal resistance curves of the same sample at different times in a high temperature and high humidity aging case.
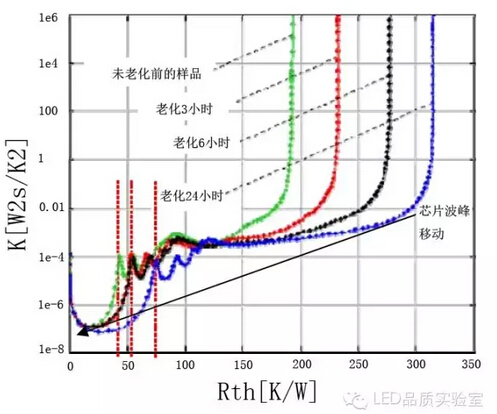
Thermal resistance drift after aging
Before and after aging, the movement of the post-chip peaks clearly shows that the delamination caused by aging leads to an increase in the thermal resistance of the chip bonding layer. For the thermal resistance test of different stages of the sample, the thermal resistance change of each layer structure can be obtained, and the aging mechanism can be analyzed according to the change, thereby improving the heat dissipation performance of the product.
5. Measurement of contact thermal resistance
As semiconductor manufacturing technology continues to mature, the thermal properties of thermal interface materials have become a bottleneck restricting high-performance packaging products. The size of the contact thermal resistance is closely related to the material and the quality of the contact. Conventional contact materials or methods are: (1) thermal adhesive; (2) thermal pad; (3) screw connection; (4) dry contact. The figure below shows a special test for contact thermal resistance.
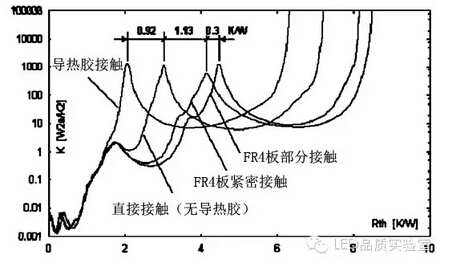
Thermal resistance of different contact modes
It is found from the above figure that the size of the contact thermal resistance is not only related to the contact material, but also related to the quality of the contact. The greater the thermal conductivity of the contact material, the smaller the contact thermal resistance. The better the contact quality, the smaller the contact thermal resistance.
6. Examples of thermoelectric parameter characteristics
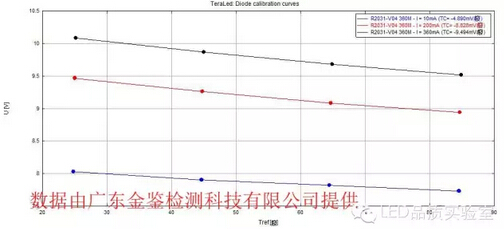
Voltage temperature curve
As can be seen from the above figure, as the temperature rises, the voltage of the sample LED decreases linearly.
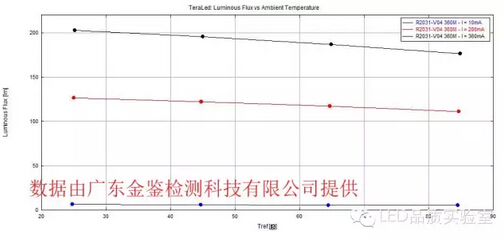
Luminous flux temperature curve
As can be seen from the above figure, as the temperature rises, the luminous flux of the sample LED decreases linearly.
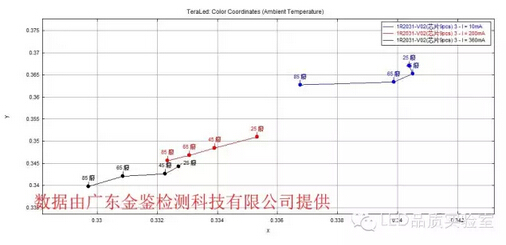
Color coordinate drift curve
As can be seen from the above figure, as the temperature rises, the color coordinates of the sample LED will drift toward the high color temperature.
Editor: Li Jie
Ultra-thin Insulation Submersible Motor Winding Wire
This products is made of solid copper wire conductor, multi-layer modified materials insulation jacket. It has fine performance for water-resistant, mechanical, electric conducting. It is used to water-filled submersible motor with ultra-thin insulation demands and applied to standard of environmental-friendly.
The conductor is used the standard of GB/T3953, and applied to JB/T4014 standard.
The product can be made according to customers` ultra-thin demands for high-temperature, high-voltage, frequency-conversion, anti-corrosive.
Ultra-Thin Insulation Submersible Motor Winding Wire,Thin-Insulation High-Voltage Submersible Winding Wire,Insulation High Voltage Submersible Wire,Surplus Thin Insulated Submersible Winding Wire
HEBEI GUOQIAN WIRES CO., LTD , https://www.guoqianwires.com