With industrial pollution and environmental damage becoming increasingly serious, water treatment is one of the areas that has received much attention for a long time. It is an important means to improve the living environment of residents and improve the health of the people. At the same time, with the development of science and technology, people have higher and higher requirements for the degree of automation of equipment. The automatic control of water system has been accepted, promoted and popularized, and has been rapidly developed. The automatic control of the water treatment facilities not only reduces the labor intensity of the water treatment operators, but also reduces the number of operators and achieves staff reduction and efficiency. More importantly, it can ensure the water quality after water treatment, and also ensure the safe operation of the equipment, extend the service life of the equipment, and thus reduce the production cost. It can be said that it is a good thing in one fell swoop and is the development direction of China's water treatment industry.
This article refers to the address: http://
Background of the project:
Give &TImes;&TImes; the company implements a purification system for domestic water and drinking water.
Water treatment principle part:
The water treatment method used in this system:
Aeration:
Role: remove dissolved gases.
Chemical oxidation
Role: oxidize inorganic cations, destroy organic matter.
Particle layer filtration
Role; removal of micelles and particulate suspension
4) Storage
Function; adjust the amount of water, water self-cleaning
5) Irradiation
Role: kill bacteria, viruses, catalytic oxidation.
6) Activated carbon adsorption
Role: remove dissolved organic matter.
7) Ion exchange
Role: remove dissolved salts.
8) Microfiltration
Role: remove fine particles
9) Reverse osmosis
Role: remove dissolved salt components.
Flow chart
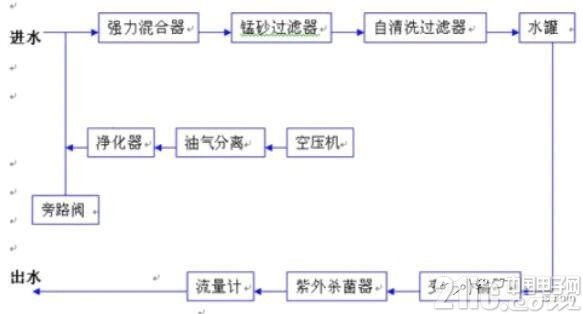
This system adopts Zijinqiao monitoring configuration software as the upper computer software and PLC for control and display.
1) Zijinqiao monitoring configuration software
The powerful configuration interface of Zijinqiao monitoring configuration software can directly simulate and display images, monitor the working conditions of the site, work procedures, real-time data and handling of unexpected situations.
2) PLC programmable controller
PLC (ProgrammableLogicController) is a member of the computer family. Designed and manufactured for industrial control applications, it is mainly used to replace logic to achieve logic control. With the development of technology, the function of this device has greatly exceeded the scope of logic control. Therefore, the main features of PLC: (1) High reliability; (2) rich I / O interface module; (3) using modular structure; (4) simple installation and convenient maintenance. Used in the aerospace industry, agriculture, water conservancy projects and other fields.
System architecture diagram:
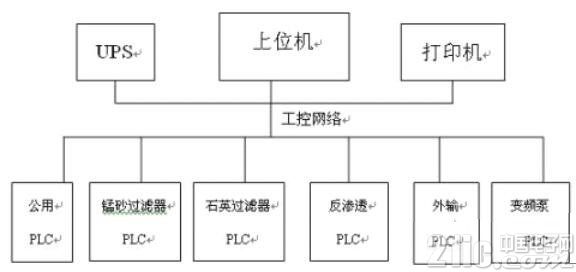
The automatic control of purified water treatment includes the following aspects:
1) The device automatically starts and stops
When the liquid level of the production tank after the water production process is low, the water production process equipment is automatically started. When the tank level is high or there is no water in the previous process, it can be set to stop automatically, or switch the series, or the water production process cannot be started. In addition, in the event of an alarm or other malfunction, it will automatically stop and switch the equipment series.
2) Automatic cleaning of equipment
When the timer, differential pressure gauge, and cumulative flow meter on the water-making equipment reach the set value, the equipment automatically stops running and realizes the cleaning back-flushing process.
3) Automatic display function
Real-time display of the health of the device and control on the configuration interface.
4) Automatic protection function
No water, failure will automatically protect.
5) Automatic constant pressure water supply
Mainly at the terminal exit, some systems require constant pressure water supply.
Specific implementation method:
The automatic control is mainly implemented by the programmable controller PLC, but even the water control system that can be automatically controlled can be manually controlled and can be selected according to actual needs.
1) Water tank control
Control has some common features, generally set high, medium high, low, low and four liquid level switches.
When the tank level reaches the high level, stop the water.
When the tank level reaches the medium to high level, everything works normally.
When the tank level reaches the medium to low level, a signal should be initiated to make the front stage water.
When the water level of the water tank reaches the low liquid level, the water pump of the lower stage is turned off, and the equipment of the latter stage is stopped to prevent the water tank from being evacuated, the water pump burned out, and an alarm signal is issued at the same time.
2) Valve control
This device uses a solenoid valve to change the process of water production and backflushing by automatically controlling the opening or closing of the solenoid valve.
Solenoid valve characteristics
1 It has the advantages of convenient use, quick opening and closing, stable performance, etc., and implements remote and automatic control.
2 is a pilot-operated or double-open valve normally closed electromagnetic valve. When the power is not energized, the pilot valve port and the pilot valve movable iron core are in a closed state under the action of the self-weight and the spring.
3 When energized, magnetic force is generated, and the movable iron core is attracted by the electromagnetic force to overcome the pressure of the self-weight and the pilot spring. The force above the diaphragm is reduced and lower than the force under the diaphragm. The diaphragm is in poor power. Under the action of the self-weighted spool spring, the main valve is opened and the solenoid valve is open.
4 When the power supply is disconnected, the magnetic force is eliminated, the pilot valve port is closed, the valve diaphragm is closed by the downward pressure difference, the main valve is closed, and the solenoid valve is closed.
3) Control of manganese sand filter
When the manganese sand filter is required to start running, the PLC sends a signal. When the working process is switched, the manganese sand filter should be timed backwashing and backflushing.
4) Control of quartz sand filter
The control of the quartz sand filter is the same as that of the manganese filter. It will not be repeated.
Control of variable frequency constant pressure water supply
Pump control
Here we are using the variable frequency pump, talk about the control of the variable frequency pump.
Generally, the power of the pump is constant, and the flow rate is inversely proportional to the pressure. The larger the flow rate, the smaller the pressure. However, there will be some cases where the user's water consumption changes greatly, and the pressure will change at this time. The water consumption is small and the pressure is small; the water consumption is small and the pressure is large. However, the user also requires constant pressure water supply. At this time, a pressure sensor is arranged in the pump outlet pipe to transmit the signal to the PLC. The PLC controls the frequency converter to change the pump speed to adjust the water flow rate, thereby keeping the pump water pressure stable and achieving constant pressure. Water supply. There is also a benefit, that is, energy saving.
Specifically, through the pressure transmitter installed on the outlet pipe network, the outlet pressure signal is changed to a standard signal of 4-20 mA, and sent to the port of the PLC for PID adjustment, and the operation is compared with the given pressure parameter to obtain a Adjust the parameters and send them to the inverter. The inverter controls the speed of the water pump and adjusts the water supply of the system to keep the pressure in the water supply system pipe at a given pressure. When the water consumption exceeds the water supply of one pump, it passes through the PLC. Control the switch to add and subtract pumps. The amount of water used by the root is controlled by the increase and decrease of the number of working pumps controlled by the PLC and the speed regulation of the pump by the frequency converter to achieve constant pressure water supply. When the water supply load changes, the voltage and frequency of the input motor also change, thus forming a closed-loop control system based on the set pressure. In addition, the system also has a variety of functions, especially the hardware / software backup pump function, fully guarantee the timely and normal water supply of the pump.
Control of purified water for drinking water:
It adopts PLC control and adopts intelligent microcomputer for data processing.
3) The control mode adopts manual and automatic control modes.
1 manual
The switch of each control valve and the start and stop of the water pump can be controlled by the button on the control panel.
2 automatic
The entire water line, the operation of the process, start and stop, are automatically controlled by the PLC and are not subject to human intervention.
Main control output function
The system can control the automatic work and automatic procedures of the intermediate tank, lift pump, activated carbon, softener, reverse osmosis, pure water irrigation and other units according to various signals and processes.
The function of the host computer monitoring configuration software:
The system adopts the Zijinqiao monitoring configuration software of Zijinqiao Software Co., Ltd., and enables the PC to communicate with the PLC through the RS-232 serial communication port.
The process can be monitored in real time through the Zijinqiao configuration software. The database of Zijinqiao configuration software provides various types of points, which facilitate the control of various types of points throughout the entire water treatment process. The control of the solenoid valve by the host computer must be carried out through the digital value output block, and the control of each valve corresponds to the corresponding digital output node. Therefore, the host computer can not only accept the control signal from the PLC and display it in the form of animation, but also can send control commands to the PLC through the communication port to control the scene. Through the analog block, the host computer can read the real-time data of the pressure and flow collected from the instrument at the control station through the communication port, display it in real time on the host computer, and alarm the system when the fault occurs. You can also save history, draw historical curves, automatically generate reports, and more.
Conclusion:
It adopts the control scheme designed in this paper to automatically control it, and all the indicators can meet the process requirements and achieve better control effects.
The best just got better. Now introducing Fume ULTRA, a new exclusive vape product with the same superior quality of the fume EXTRA, with elevated features. Now featuring 2500 puffs, generous 1100 battery, 5 percent nicotine, all compiled in the same sleek model of the FUME. Fume Ultra comes in 18 ultra smooth flavors, with effortless draw activation and ultra potent clouds.
Device Details:
Nicotine Strength: 5.0%
Battery Capacity: 1100mAh
Puff Count: 2500+ Puffs
22 Flavors
Disposable Vape Pen, Vape, Vape Kit, Fume Ultra
Shenzhen Essenvape Technology Co., Ltd. , https://www.essenvape.com