With the increasing demand for energy saving and emission reduction and driving experience, the automobile manufacturing industry has quietly set off a “lightweight trendâ€. Reducing the weight of the car not only reduces fuel consumption (it is reported that every 10% of the car's weight, fuel consumption will be reduced by 6%-7%), reducing carbon dioxide emissions, but also can improve acceleration performance, shorten braking distance, and ultimately improve the driving experience. Therefore, automobile lightweighting has become a new goal pursued by domestic and foreign automakers.
The most effective way to achieve lightweight vehicles is to use lightweight materials. Of course, optimizing the structure of the car and adopting advanced sheet metal splicing technology will also help the car to achieve lightweight.
Compared with traditional steel, currently available automotive lightweight materials are aluminum alloy, carbon fiber, magnesium alloy, titanium alloy, plastic, etc. Among them, aluminum alloy and carbon fiber are most favored by automobile manufacturers, such as Audi, Renault, BMW, Bugatti. Some of the high-end cars are used.
Carbon fiber is a material that is woven according to a certain rule of ultra-fine wool with high carbon content. It is light in weight, high in strength and high in temperature. It can be used from engine system and transmission system to braking system and chassis. The system as well as the body and accessories.
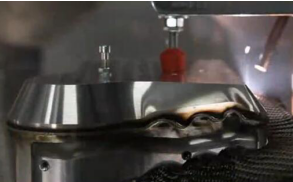
The strength of carbon fiber is larger than that of steel and it is difficult to process. The key to using lasers to process carbon fibers is the trade-off between processing quality and processing speed – both fast processing and small heat affected zones. High-power infrared lasers and ultra-fast lasers can be used to process carbon fibers, but infrared laser processing has a large heat-affected zone, while ultra-fast laser processing is slow. In contrast, high-power UV lasers can be used in these two indicators. A good balance is achieved, such as Spectra-Physics' high-power Quasar UV laser, which cuts 250μm carbon fiber at 70mm/s with a heat-affected zone of less than 15μm. Trumpf's TruDisk, TruFlow, TruMark and other products also have excellent performance in carbon fiber cutting, punching and marking. Of course, the specific processing light source to be used depends on the specific processing requirements.
The laser can cut, punch, score and mark the carbon fiber material, and can also be used for trimming, cleaning, and grafting and ablation of the molded part.
It is reported that the Oak Ridge National Laboratory is studying a carbon fiber laser surface treatment process, which laser treatment of the surface of the carbon fiber layer before bonding, which will help the bonding of the carbon fiber layer, and ultimately be more environmentally friendly and lower. A higher quality carbon fiber material is produced in a cost manner.
Aluminum alloy is one of the most lightweight materials currently used in automobiles. It is light in weight, good in corrosion resistance and easy to process. It will replace steel more and more. The use of aluminum alloy will spread over more and more parts such as frame, door, cylinder block, cylinder head and hood.
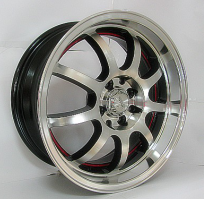
The biggest challenge of laser processing aluminum alloys is the reflectivity of aluminum alloys and their thermal conductivity. In view of this, the surface of the aluminum alloy can be treated first, and the high power density can be used in a very short time to reduce the reflection and heat conduction problems. In the aspect of aluminum alloy welding, continuous laser mode welding is usually used. The Han family laser has a continuous laser solution specially designed for aluminum alloy welding. In addition, Trumpf's TruDisk laser combined with its IPFO intelligent galvanometer and weld tracking sensor to achieve aluminum alloy lap joints, corner joints, wire filler welding and other forms of welding.
In addition, the application of various engineering plastic materials in automobiles is also increasing. From the instrument panel, the seat, the door trim to the rearview mirror, the fender and other accessories, plastic materials are used. Laser technology such as cutting and welding can also be used in the processing of plastic materials.
In addition to using the above lightweight materials to achieve lightweight vehicles, it can also help the car to reduce weight in terms of processing optimization. For example, laser welding of sheets can reduce the overlap of the sheets and thus reduce the weight. In addition, the market development of electric vehicles in the past two years is also very fast. We often see that there are charging piles “quickly standing up†next to the parking spaces in the community. Lightweight development will use more lithium-ion batteries, while in lithium. In the production of batteries, a large number of welding processes are carried out with lasers.
The lightening of cars is a general trend. Although this process cannot be achieved overnight, the urgent pressure from energy and environment, as well as consumers' pursuit of safety and better driving experience, are prompting people to develop new ways. Realizing light weight of automobiles; laser as an advanced processing technology in modern manufacturing has basically become a standard tool in the automobile manufacturing industry. The continuous emergence of processing demand will inevitably lead to continuous exploration and breakthrough in the field of laser technology. Lasers will become a good helper on the road to lightweight vehicles.
To understand the latest applications of laser processing technology in automotive lightweight and more fields, please pay attention to the 2017 South China Laser Show. At that time, Dahai Laser, TRUMPF, Huagong Laser and other domestic and overseas companies will showcase their advanced laser processing technology.
Newmax Electronics Co.,Limited , https://www.advvape.com