Based on the working principle of the tire building machine and the analysis of the various components of the servo system, a set of forming machine servo control system is designed.
1 IntroductionWith the vigorous development of the domestic economy, the car has already completed the new generation of travel tools into thousands of households. As an indispensable tire for automobiles, it is bound to become a consumer product of a car family, because its various applications have broad market prospects. This demand has driven China's tire and rubber industry. As a result, international and domestic tire manufacturers have landed in China to invest and build factories to expand production scale to meet the growing demand for tires. One of the most important aspects of tire production is the formation of tires. Manufacturers of tire building machines in various countries have tried their best to develop efficient, accurate and fast tire building equipment. In recent years, with the rapid development of microelectronics technology, power electronics technology, computer technology, modern control technology, material technology and the gradual improvement of motor manufacturing technology, servo technology has ushered in new development opportunities. The servo system is traditional. Step servo and DC servo have developed into a new generation AC servo system with permanent magnet synchronous motor and induction motor as servo motor.
The servo system is an important part of the automatic control system. Its performance directly determines and affects the rapidity, stability and accuracy of the automatic control system. The combination of machine, electricity and liquid has become the main technical basis of industrial automation. A servo control system is used to accurately follow or reproduce a feedback control system for a process. In many cases, the servo system refers to a feedback control system in which the controlled amount (output of the system) is mechanical displacement or displacement velocity and acceleration, and its function is to make the mechanical displacement (or rotation angle) of the output accurately track the displacement of the input ( Or corner). There is no principle difference between the structural composition of the servo system and other forms of feedback control systems. The main task of the servo system is to transform, control and power amplify the signal according to the requirements of the control command, so that the torque, speed and position of the output of the driving device can be flexibly and conveniently controlled.
Due to the fast response, high speed and high positioning accuracy of the servo motor, this type of motor is generally used as a feed motor and a small plate control motor. With the continuous pursuit of molding machine precision and molding machine speed in the molding machine market, UV flatbed molding machines will gradually be introduced to the market. With the development of UV flatbed molding machines, the matching servo motors will also be upgraded. In the high-end molding machine market, AC servo motor systems will be the mainstay. So many advertisers finally choose a molding machine. In order to cater to the domestic market, some manufacturers began to develop and produce their own branded molding machines based on the introduction of foreign advanced technology.
2, tire molding machine introductionThe complete system of tire forming machine equipment consists of PLC, touch screen, servo control system and actuator. The molding of the tire is based on the size requirements of the tire, and the curtain and the tape of the hanging rubber are cut into a certain long dimension, and after being fitted, the tire blank is formed by extrusion. Therefore, according to the requirements of the molding process, the equipment generally includes a carcass laminating drum, a belt drum, a forming drum, an inner ring transfer ring, an outer ring transfer ring, a belt supply rack, a curtain supply rack, and a crown belt layer. Material rack, composite glue. The transmission requirements of these devices are fast and the positioning of the position is accurate. At the same time, when the main drum is rotating, its auxiliary equipment is required to be fed synchronously. Therefore, the transmission of these devices uses a servo motor. In the auxiliary drive of the feeding frame, cutting and other transmissions, there are related ordinary motors that need to be controlled. There are also many switch points and sensor points in each rack. There are also some pneumatic units that need to be controlled. In addition, a high-efficiency molding machine must be able to manufacture tires of different sizes and sizes, that is, on the man-machine interface, various production processes can be invoked, various production processes can be executed, and the production status can be displayed and recorded. Some manufacturers also require remote debugging, monitoring and so on. Therefore, designing an efficient, simple structure, simple installation and commissioning, and controlling the centralized and decentralized control system is the goal that the automatic control manufacturers are constantly pursuing.
In the tire building machine there are many pneumatic components, the inverter needs to be controlled. In order to reduce the complicated installation, we adopt CAN bus communication technology, that is, one cable controls multiple inverters, automatic valve island, multi-point sensor unit, and more acquisition. Encoder data. This design saves a lot of cable laying because it saves a lot of analog and high-speed counting of the template, which makes the price quite competitive. Reliability is greatly improved. At present, encoders with CAN bus enable the transmission of data without worrying about the effects of interference.
3.1 motion control card
The motion control card is a high-level control unit that can control the servo motor. It is based on the PC bus and uses a high-performance microprocessor (such as DSP) and a large-scale programmable device to realize a multi-axis coordinated control of multiple servo motors. The performance of the stepper / servo motor motion control card includes pulse output, pulse count, digital input, digital output, D / A output and other functions, it can send continuous, high frequency pulse train, by changing the frequency of the pulse to control The speed of the motor changes the number of pulses to control the position of the motor. Its pulse output mode includes pulse/direction, pulse/pulse mode. Pulse counting can be used for encoder position feedback, providing accurate machine position and correcting errors during transmission. Digital input/output points can be used for speech limits, home switches, and more. The products are widely used in industrial automation control fields where precise positioning and fixed length position control systems and PC-based NC control systems are required. Specifically, the underlying software and hardware that implement motion control are integrated to provide various speed and position control functions required for servo motor control. These features can be easily called from a computer.
The motion control card not only sends pulses to the motor driver, but also receives the number of pulses fed back by the servo motor encoder, and also receives the grating scale feedback signal to control the speed of the servo motor. The servo drive must have a data cable connection to the motion control card, and it must also be connected to the outlet power supply.
If your motion control card is a good card, the servo refresh rate can meet the requirements, you can directly connect the encoder feedback to the motion control card to form a whole closed loop. If there is a high requirement for accuracy, a double closed loop can be used. The motion control card controls the movement of the motor to an accurate position according to the position where the xy platform is required to operate.
3.2 PC bus
The existing implementation of the open CNC system mainly adopts the combination method of PC and numerical control system. The PC as the upper computer realizes more complicated network communication, human-computer interaction and other functions. The numerical control system acts as the lower computer to input the upper computer input. The parameters are processed and sent to the execution component for execution. At the same time, the feedback information of the detection system is uploaded to the upper computer for real-time monitoring, and the coordination work between the modules does not interfere with each other, which brings convenience to the system upgrade.
The core of the open system dynamic controller is DSP. It has the characteristics of fast calculation speed and support for complex motion algorithms, which can meet the requirements of high-precision motion control. Therefore, multi-axis dynamic control cards with DSP as the core are more and more widely used. The ground is applied in the motion control system, and the multi-axis dynamic control card is inserted into the expansion slot of the PC to form a high-precision motion control system. The position feedback signal acquisition, closed-loop control calculation and control quantity output are all controlled by the dynamic control card. Completion greatly improves the calculation speed and control response speed, and solves the resources of the industrial computer from the cumbersome data collection and calculation, so that the management of the entire control system can be better implemented.
OREMA QTF series AGM start-stop batteries are at the forefront of lead-carbon technology, tailored for vehicles with start/stop and mild hybrid systems. Ideal for caravans, boats, motorhomes, and more, these batteries showcase exceptional charge acceptance and cold starting capabilities. Experience the difference with OREMA's advanced lead alloy formula, specifically designed for today's demanding automotive applications.
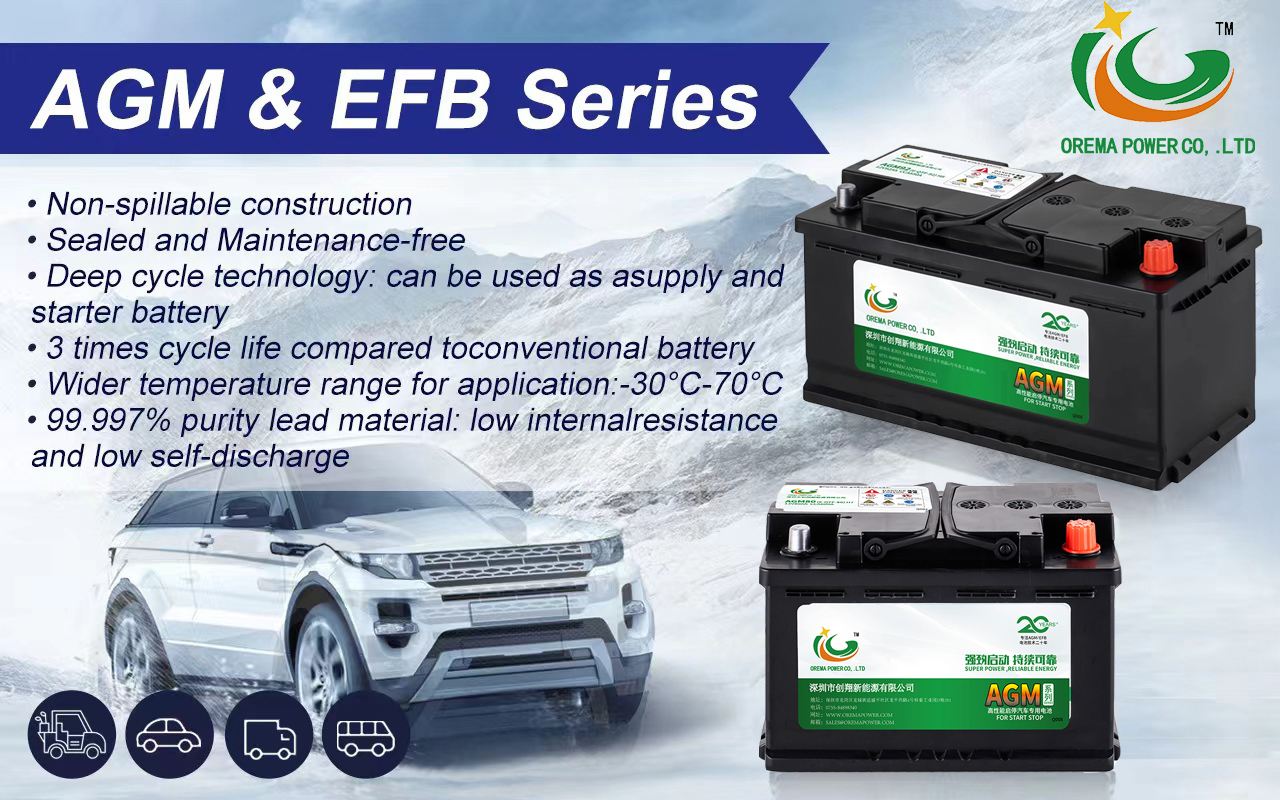
Key Features of OREMA 12V AGM car batteries:
Enhanced Durability: Crafted with reinforced design, the battery casing and cover are made of high-strength, heat-resistant PP engineering plastic, ensuring longevity and reliability under various conditions.Innovative Construction: Equipped with imported pocket-type PE separators, our batteries effectively prevent short circuits due to active material shedding, resulting in low internal resistance and high current discharge.
Advanced Safety Features: Special anti-acid explosion-proof patches are employed to isolate potential sparks, making our batteries safer for everyday use.
Patented Technology: The patented deep cycle positive paste and negative lead carbon technology significantly extends the battery's cycle life.
Efficient Design: Unique labyrinthine cap design allows for smooth electrolyte recirculation, minimizing water wastage and prolonging battery life.
Cutting-edge TTP Welding: Advanced TTP welding technology ensures minimal internal resistance during connections.
Special Valve Design: Prevents corrosion, enhancing the battery's durability.
High Assembly Pressure: This design feature significantly extends the battery's lifespan.
Wide Temperature Range: Our batteries are functional in temperatures ranging from -30°C (-22°F) to 70°C (158°F), accommodating diverse environmental conditions.
OREMA AGM car start-stop battery core technology:
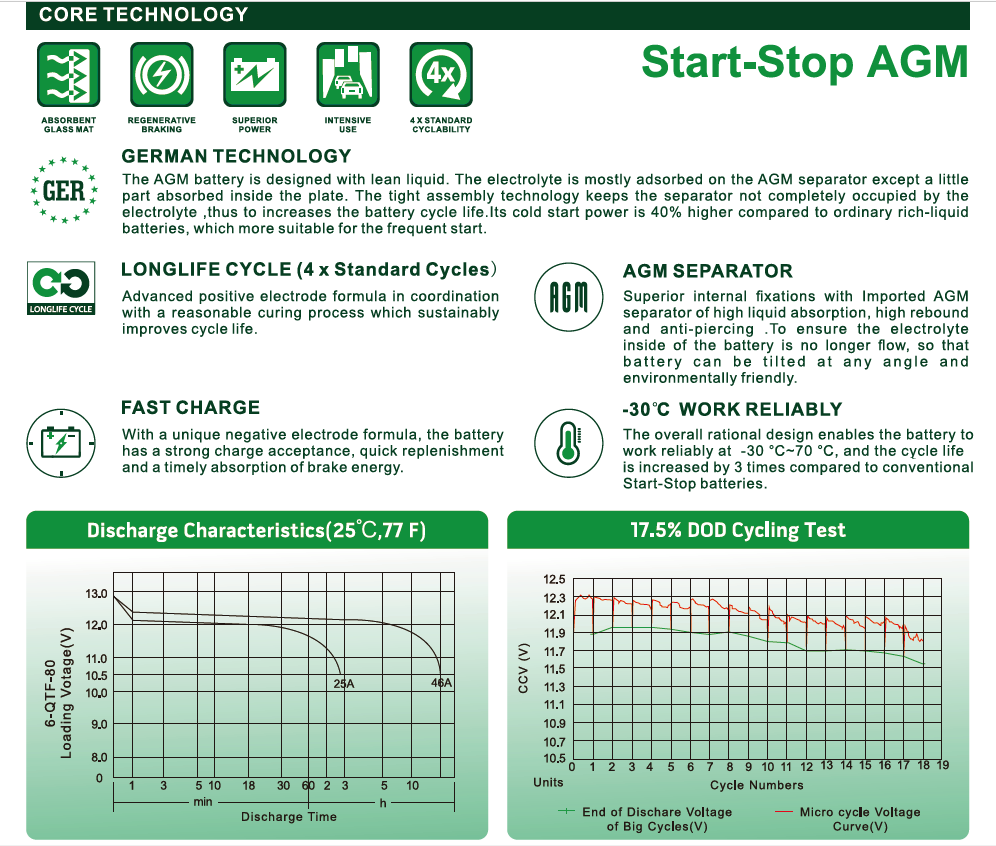
Specifications of OREMA QTF Series AGM Start-stop batteries:
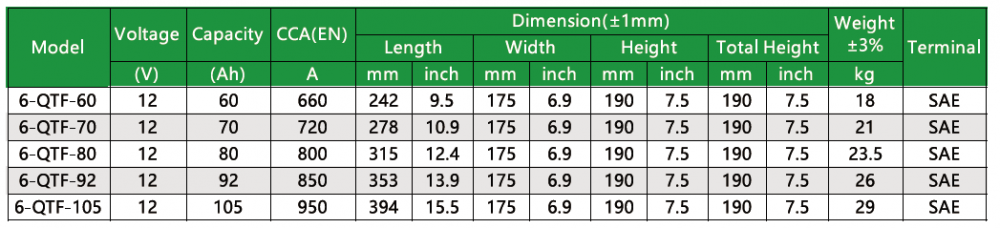
Why choose OREMA as AGM start-stop battery provider?
The upgraded lead-carbon battery technology significantly improves battery life; By adding new active substances to the plate, the charging efficiency is significantly improved; At the same time, the low water loss ensures the long-lasting stability of the battery at high temperatures.OREMA QTF series AGM automotive batteries introduce innovative technology, showing excellent instantaneous high current release performance, and its continuous casting grid technology enhances the corrosion resistance of the grid; By improving the mechanical strength of the grid, the anti-shock performance of the battery is improved.
The OREMA QTF Series AGM Automotive Battery is known for its powerful starting power, low water loss and long service life, and is specially built for vehicles requiring basic electric support. While maintaining superior performance, it provides a higher price/performance ratio. OREMA QTF Series AGM automotive batteries are designed to simplify life and add value to your car by providing more affordable and responsive battery solutions from the consumer's perspective.
Choose OREMA car batteries, which are prized for their long-lasting performance. Quality products can withstand the test of time and user inspection.
car start-stop battery,Start-stop battery,AGM Start-stop batteries,AGM battery for car,12V AGM car batteries
OREMA POWER CO., LTD. , https://www.oremapower.com